
Food waste is the second largest category of municipal solid waste (MSW) sent to landfills (Environment Protection Agency, n.d.). Over 30 million tons of food waste is sent to landfills each year and much of this goes into landfills where it produces methane, thus contributing to global warming. The most important reason that food waste should be recycled is for capturing the energy content. Food waste is highly biodegradable and has a much higher volatile solids destruction rate (86-90%) than biosolids. In fact, in a study done by East Bay Municipal Utility District it was revealed that foodwaste has up to three times as much energy potential as biosolids.
As energy prices continue to climb and our nation looks towards renewable energy generation and energy independence, capturing the energy from food waste becomes more important. There are three key methods of recycling food waste into a valuable product which are In-vessel composting, anaerobic digestion, transesterification, pyrolysis and gasification.
2.2.1 In-vessel composting
In-vessel composting produce compost through the in-vessel process. The process mix food waste with garden waste, shredding it and then composting it in an enclosed system for around 2 to 4 weeks under a controlled temperatures of up to 70°C to speed up the process as well as to ensure any harmful microbes are killed off. The material is then left outside to mature for a further 1 to 3 months with regular turning and checks to ensure quality before going on to be used as soil conditioner.
2.2.2 Anaerobic Digestion
Anaerobic Digestion uses microorganisms to break down food waste, animal manure, slurries and energy crops in the absence of oxygen, inside an enclosed system. As it breaks down it gives off methane, which is collected and converted into biogas and used to generate electricity, heat or transport fuels. It also creates a nutrient-rich digestate that can be used as a fertiliser for agriculture and in land regeneration.
2.2.3 Transesterification
Transesterification is a chemical reaction used for the conversion of vegetable oil such as soya, canola, jatropha, sunflower seed, algae, etc., animal fats and oils being reacted with short-chain alcohols (typically methanol or ethanol) to biodiesel in presence of a catalyst like lye. After the chemical reaction, various components of vegetable oil break down to form new. Common feedstock used in biodiesel production include yellow grease (recycled vegetable oil), "virgin" vegetable oil, and tallow.
2.2.4 Pyrolysis
Pyrolysis is chemical reaction. This reaction involves molecular breakdown of larger molecules into smaller molecules in presence of heat. Pyrolysis is also known as thermal cracking, cracking, thermolysis, depolymerization, etc. Pyrolysis is used heavily in the chemical industry, for example, to produce charcoal, activated carbon, methanol, and other chemicals from wood, to convert ethylene dichloride into vinyl chloride to make PVC, to produce coke from coal, to convert biomass into syngas and biochar, to turn waste into safely disposable substances, and for transforming medium-weight hydrocarbons from oil into lighter ones like gasoline.
2.2.5 Gasification
Gasification is a partial oxidation process whereby a carbon source such as coal, natural gas or biomass, is broken down into carbon monoxide (CO) and hydrogen (H2), plus carbon dioxide (CO2) and possibly hydrocarbon molecules such as methane (CH4). The input to gasification is some form of solid carbonaceous material— typically biomass or coal. All organic carbonaceous material is made up of carbon (C), hydrogen (H), an oxygen (O) atoms– though in a dizzying variety of molecular forms. The goal in gasification is to break down this wide variety of forms into the simple fuel gasses of H2 and CO— hydrogen and carbon monoxide.
2.3.1 In-vessel composting
Susteco AB, a Swedish based company, provides solutions for on-site composting of food waste (Swedish Cleantech, n.d.). Susteco AB manufacture the Big Hanna composter that compost with a unique flow-through system giving our customers a simple and practical way to compost food waste on site. The Big Hanna produces the most mature compost in the market and is therefore suited to be installed in highly populated areas. Big Hanna Composter model T480 is an on-site composter taking care of 800-2400 kg of food waste per week. Food waste is loaded at the front of Big Hanna Composter and compost is automatically discharged to the rear.
2.3.2 Anaerobic digestion
At Dagenham Plant, United Kingdom, promoting the cluster economy concept, the Mayor of London’s office established the London Sustainable Industries Park14. Part of the 60 acres set aside with a £30 million investment by the Mayor of London, houses a £21 million AD system. According to Ryan C. Davis. (2014), he Anaerobic Digestion system has a capacity of 50,000 tonnes of organics per year with a majority of this being food and green waste from the City of London and nearby boroughs. The biogas is sent to a CHP system where 1.4 MW of electricity is sold on the national grid, and 1.15 MW of thermal energy is utilized by nearby facilities. Income for the facility is expected to come largely from feed-in tariffs and tipping fees, however, the plant is expected to produce 14,000 tonnes of compost which is then to be sold for agricultural purposes.
2.3.3 Transesterification
Desmet Ballestra is an engineering group operating all over the world in the oils & fats industry and various areas of the organic/inorganic chemical industry (Desmet Ballestra, 2014). Desmet Ballestra has developed a continuous transesterification process to produce Diesel-Fuel Substitutes (BIODIESEL) starting from a wide range of vegetables oils of various purity (crude/neutral/refined), including exhaust and “fried” oils from edible/food applications without the need for a full refining step up-stream. Desmet Ballestra is nowadays in a position to design and to supply Biodiesel production plants sized in a wide range of production capacities (from 10,000 up to 200,000 T/y), coping with the most stringent international standard specifications.
2.3.4 Pyrolysis
Pacific Pyrolysis Pty Ltd has developed, and is commercialising, slow pyrolysis technology to deliver waste to energy and biochar solutions (Environment XPRT, n.d.). The technology to convert non food biomass into renewable energy and a proprietary biochar called Agrichar, that has been proven by independent trials to increase food production and sequester carbon over long periods of time. The company owns 100% of the intellectual property, global development and commercialisation rights of the technology including the integrated pyrolysis demonstration plant located at Somersby. Biochar produced from the Pacific Pyrolysis process can also be utilised as a green fuel and in some cases a metallurgical reductant. Biochar produced from softwood increased its calorific value from 18 MJ/kg to 31 MJ/kg. The char can be then be pelletised resulting in pellets with an energy density of 24 MJ/m3, compared to the 13 MJ/m3 energy density of cold pelleted softwood sawdust. This has significant implications on shipping costs per MJ of energy.
2.3.5 Gasterification
PRM Energy Systems, Inc. delivered KC Gasification system is world renowned as the premiere technology for biomass gasification. PRME Systems have operated around the clock for over 32 years in high demand industrial applications. PRME has gasified more biomass than all other gasification technologies combined and are successfully operating in high demand industrial applications on five continents converting over 8.5 million tons of biomass and other waste fuels to clean energy. The PRME Technology converts solid fuels to combustible gases that are used like natural gas to fire boilers, dryers, kilns, furnaces, thermal oxidizers and IC engines. PRME Gasification Systems are available in a wide range of sizes to gasify from 30 to 2,000 tons per day (PRM Energy Systems Inc., 2015). Gasification can enhance the U.S. and world energy portfolio while creating fewer air emissions, using less water, and generating less waste than most traditional energy technologies. Reducing the environmental impact of waste disposal because it can use waste products as feedstocks—generating valuable products from materials that would otherwise be disposed as wastes.
2.0 Literature Survey
2.1 The varieties of available technologies
2.2 The reactions involved
2.3 Researchers or practitioners that made these technologies successful
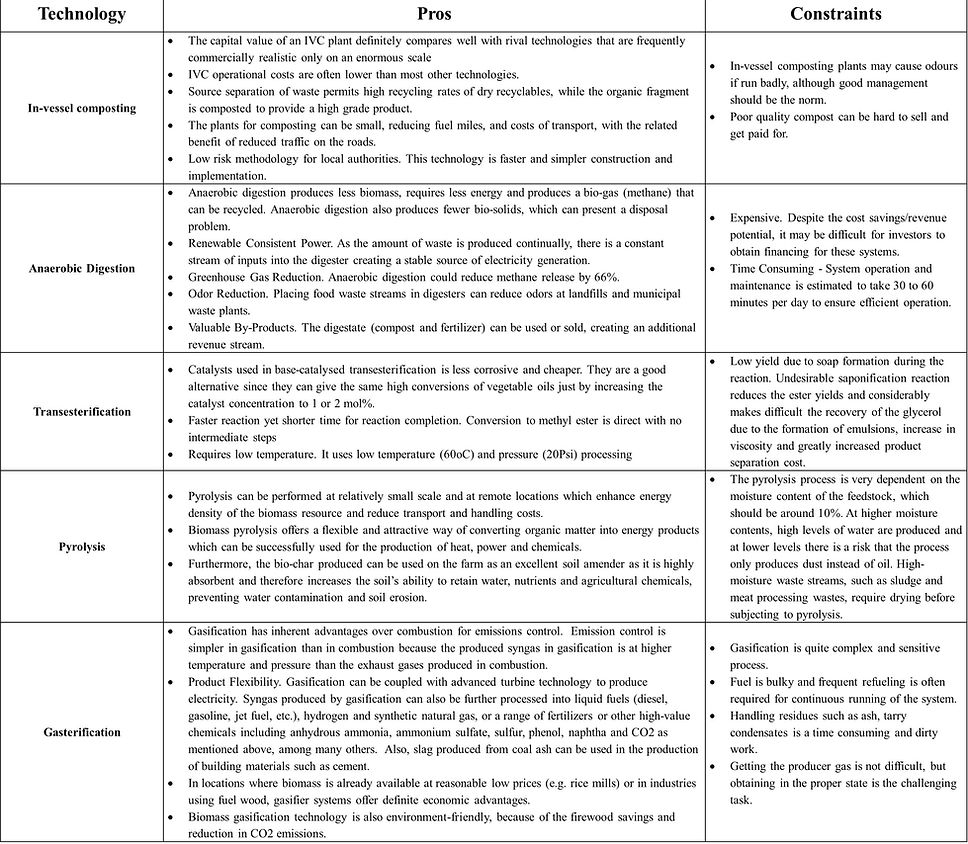